Shim
What Are Shims

How Shim Stacks Work in Shock Absorbers
Why choose MAX shims

Quality Assurance: Our products are TS16949 and ISO9001 certified, ensuring that every auto part you get meets the highest quality standards. We strictly follow the international quality management system and implement a comprehensive quality control process to ensure product reliability and durability.
Expertise: With many years of industry experience, we have a deep understanding of customer needs and market dynamics. Our team of experienced professionals can provide you with targeted solutions to help you stand out in the fiercely competitive market.
Customer Satisfaction: We always put customer satisfaction first, uphold the principles of honesty and integrity, and ensure that you get the best service experience in every transaction. We value long-term cooperative relationships with our customers, actively listen to your feedback, and continuously improve our services to meet your expectations.
Production capacity and technological advantages
The company currently has 30 high-speed stamping production lines, as well as more than 60 other stamping equipment and special equipment, with an annual production capacity of more than 10 billion pieces. These advanced production facilities enable us to efficiently meet customer needs and ensure high product quality and high output.
Each high-speed stamping line has extremely high production efficiency, capable of punching at a speed of 200 to 700 times per minute. This efficient production capacity not only improves our production efficiency, but also shortens the delivery cycle, allowing us to respond to market changes and customer orders in a timely manner.
We are committed to continuously optimizing our production processes and introducing the latest technologies and equipment to maintain our competitive edge in the industry. By continuously improving our production capacity and efficiency, we are able to provide our customers with more competitive products and services.
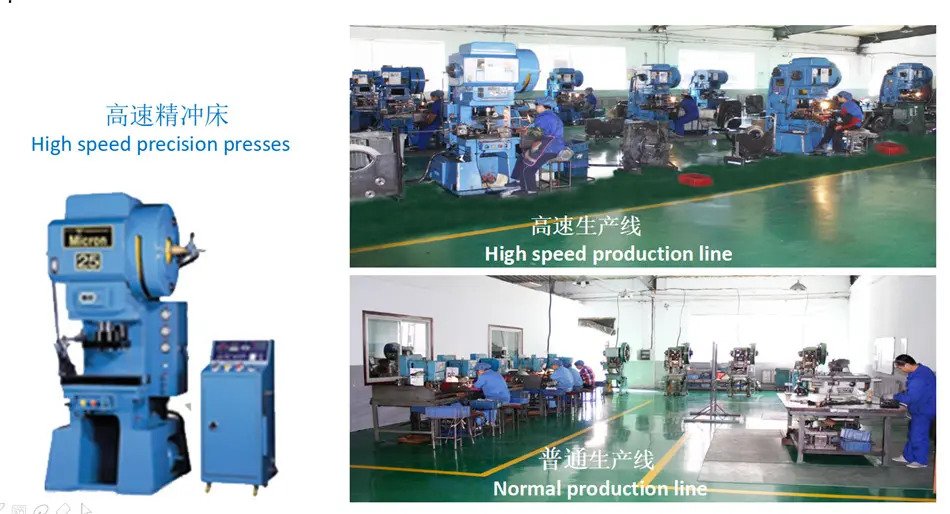

Quality Inspection and Control: Ensuring Excellent Quality
Our company uses various advanced equipment for comprehensive testing of products to ensure that every product meets strict quality standards. Our main testing equipment includes:
Contour and roughness tester: used to accurately measure the contour and roughness of product surfaces to ensure they meet design requirements.
Digital projector: Through high-precision optical measurement, it helps us quickly evaluate the size and shape of products to ensure they meet specifications.
Universal testing machine: used for testing various mechanical properties such as tension, compression, and bending to ensure the reliability and durability of products in practical use.
Micro Vickers hardness tester: measures the hardness of materials through microscope technology to ensure their performance stability in different environments.
Image measuring instrument: Using high-resolution images to accurately measure products, ensuring that every detail meets the standard.
In addition, we also conduct manual inspections to supplement equipment testing and ensure that every product undergoes strict quality control. Through these comprehensive testing methods, we are able to effectively identify and correct potential issues, ensuring that every product received by customers has excellent quality and performance. Our quality control system not only enhances the reliability of our products, but also strengthens customers’ trust in our brand.
MAX's shims series
MAX has developed seven series including concentric circle series, inner groove series, waist groove series, small hole throttling series, and disc-shaped spring. More than 5000 varieties, covering most of the automotive and motorcycle shock absorber valve plates on the market.

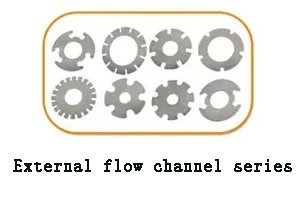
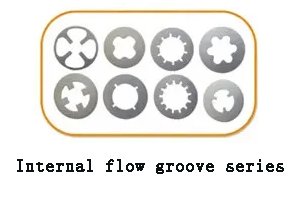
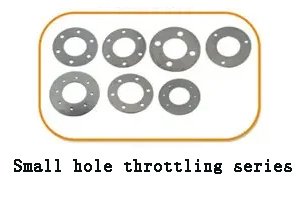
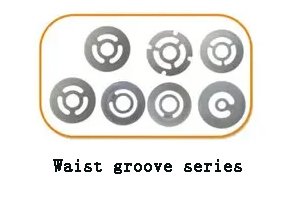

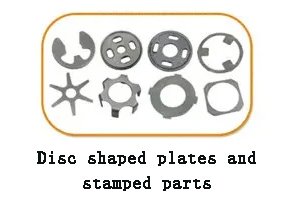
FAQS
Are you a manufacturing company or a trading company?
What is your production lead time?
What is your payment method?
What other services do you provide?
Do you have a minimum order quantity?
We can accept small orders with a minimum order quantity of 100 pieces. For large quantity orders, we also offer special discounts in order to better meet customers’ needs and budgets.