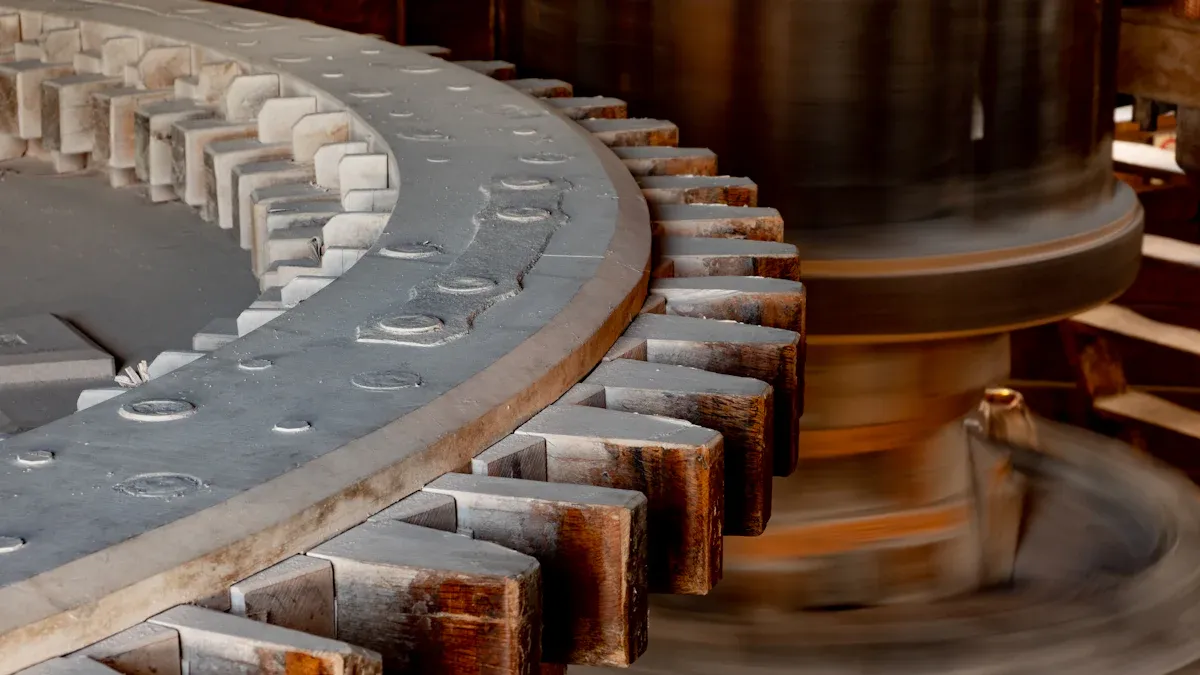
The hard chrome plated shaft is a crucial component in the industrial sector, known for its advanced surface that provides outstanding protection and greatly enhances equipment longevity. Industries depend on the hard chrome plated shaft to endure heavy mechanical stress and operate reliably in harsh environments. By extending machinery life, the hard chrome plated shaft helps ensure consistent performance and minimizes unexpected breakdowns. The global demand for hard chrome plated shafts continues to grow, with the hard chrome plating market valued at USD 1,723 million in 2022 and expected to reach USD 2,271.8 million by 2029. Comprehensive testing, including salt spray and hardness evaluations, confirms the hard chrome plated shaft’s ability to improve equipment performance and maintain optimal efficiency. Companies select the hard chrome plated shaft to maximize the durability and reliability of their machinery, supporting long-term productivity and operational success.
What Is Hard Chrome Plating for Shafts?
The Hard Chrome Plating Process
Hard chrome plating is a specialized electrochemical process that creates a tough, protective layer on metal surfaces. The process begins with careful surface preparation, including sandblasting and cleaning, to remove any dirt or oil. Technicians then use acid bath etching to activate the metal surface. After this, the shaft is placed in a chrome plating tank, where an electrical current deposits a thick layer of chromium directly onto the base metal. This layer is much thicker than decorative chrome plating, often hundreds of times thicker, and provides a durable finish.
The process can include several steps:
- Mechanical and chemical cleaning to ensure a flawless surface.
- Nickel coating as a base layer for some applications.
- Chromium plating to build up the hard, wear-resistant surface.
- Final polishing for a smooth finish.
Chrome plating works on many metals, such as steel, stainless steel, bronze, and brass. It is especially useful for shafts in hydraulic equipment, automotive parts, and mining machinery. The process restores worn parts by adding material, sometimes bringing them back to their original size. Chrome plating also makes cleaning easier and helps parts last longer in harsh environments.
Key Properties of Hard Chrome Plated Shafts
Hard chrome plating gives shafts several important properties that improve their performance and lifespan. The most notable property is high hardness, with the plating reaching between 68 and 72 HRC, which is harder than many tool steels. This high hardness means the surface resists wear and plastic deformation under heavy loads.
Other key properties include:
- Superior wear resistance, which reduces the amount of material lost during operation.
- Enhanced corrosion protection, especially in wet or salty environments.
- Lower friction, which helps machines run smoothly and reduces the risk of overheating.
- Strong adhesion and uniform thickness, even on complex shapes.
Empirical studies show that hard chrome plating can extend the service life of shafts by two to ten times compared to unplated parts. The process also improves the strength and durability of the component, making it a preferred choice in industries where reliability is critical.
Core Benefits of Hard Chrome Plated Shaft in Industrial Applications
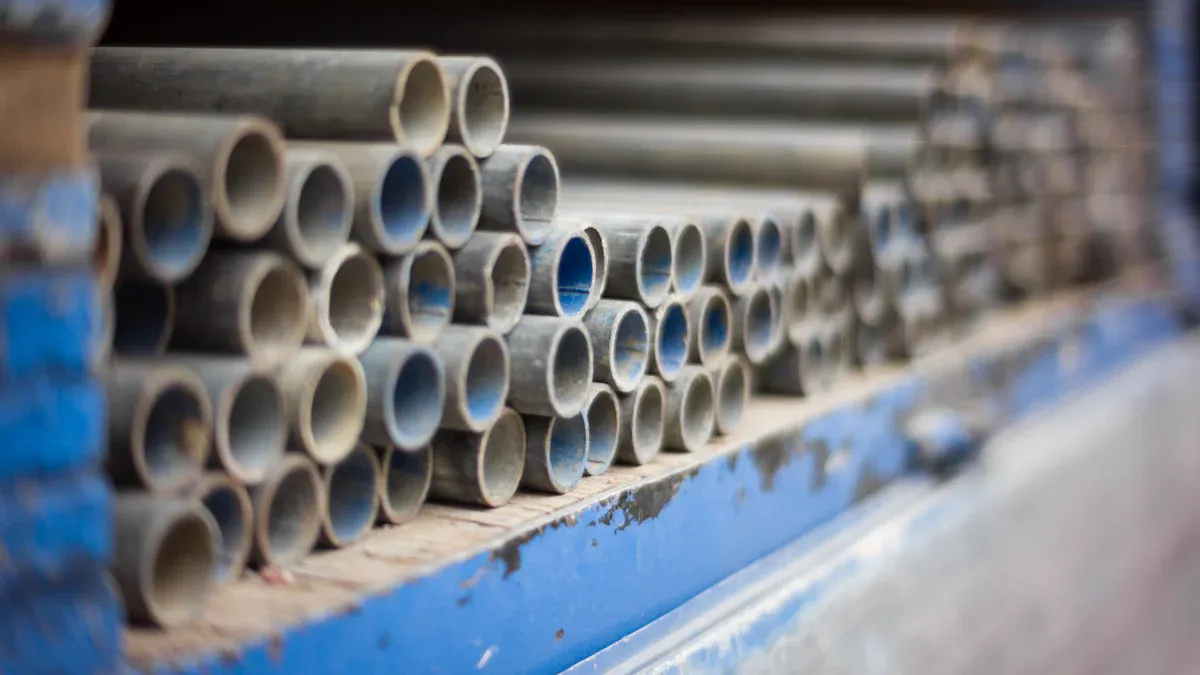
Superior Wear Resistance
Hard chrome plated shafts deliver exceptional wear and tear protection in demanding industrial applications. The chrome plating process creates a surface with high hardness, which resists abrasion and mechanical damage. An experimental study by Kir and Apay (2019) confirmed that hard chrome plating applied to low carbon steel shafts significantly increased both hardness and wear resistance. The researchers used scanning electron microscopy and microhardness testing to analyze the coating. Their pin-on-disc tests showed that optimal plating conditions, such as a 0.4 A/m² current density and a 60°C bath temperature, produced the highest wear resistance. This improvement in abrasion resistance means that equipment can withstand repeated use without significant degradation, extending the life of critical components.
Industrial applications often expose shafts to heavy loads and constant motion. Hard chrome plated shafts maintain their structural integrity under these conditions. The enhanced durability of the chrome layer reduces the frequency of part replacements and minimizes downtime. By resisting wear and tear, these shafts help companies achieve consistent performance and long-term cost savings.
Note: Hard chrome plated shafts can extend the life of machinery by up to ten times compared to uncoated alternatives, making them a strategic investment for industries that demand reliability.
Enhanced Corrosion Protection
Corrosion resistance is a vital property for shafts used in harsh environments. Hard chrome plating forms a dense, non-porous barrier that shields the underlying metal from moisture, chemicals, and corrosive agents. Salt spray testing, a standard method for evaluating corrosion resistance, demonstrates that hard chrome plating typically passes about 150 hours in these tests. Some specialized coatings can last up to 1000 hours, but even standard hard chrome plating exceeds industry benchmarks for protection.
Salt spray chamber testing simulates real-world corrosive conditions, such as those found in coastal or marine environments. This process detects microscopic defects and helps predict long-term performance. Long-term corrosion studies show that hard chrome plated shafts with a nickel underlayer can withstand up to 500 hours of salt spray exposure. These results confirm that hard chrome plating provides reliable protection and maintains the structural integrity of shafts over extended periods.
Plating Type | Test Method | Corrosion Resistance Duration | Certification/Standard |
---|---|---|---|
Cromax C® | Acetic Acid Salt Spray (ISO 9227 AASS) | 100 hours at rating 9 | EN10204 certificate 3.1 |
NiKrom 500 | Acetic Acid Salt Spray (ISO 9227 AASS) | 500 hours | – |
NiKrom 500 | Neutral Salt Spray (ISO 9227 NSS) | 1500 hours | – |
NiKrom 150 (10 µm Ni layer) | Acetic Acid Salt Spray (ISO 9227 AASS) | 150 hours | – |
NiKrom 150 | Neutral Salt Spray (ISO 9227 NSS) | 500 hours | – |
Hard chrome plated shafts comply with standards such as SAE AMS2406, ASTM B650, and MIL-C-23422. These certifications further validate their long-term corrosion resistance and suitability for industrial applications. By providing robust protection, hard chrome plating helps in extending the life of machinery and reducing maintenance costs.
Reduced Friction and Smoother Operation
A low coefficient of friction is essential for smooth and efficient machine operation. Hard chrome plating creates a surface that significantly reduces friction compared to bare steel. Measurements show that the coefficient of friction for chromium on hard steel is about 0.15 in dry conditions, which is roughly 25% that of hard steel on hard steel. This reduction in friction lowers energy consumption and heat generation, which helps prevent premature wear and tear.
Material Pairing | Dry Coefficient of Friction | Oiled Coefficient of Friction |
---|---|---|
Hard Steel on Hard Steel | 0.42 | 0.03 |
Chromium on Hard Steel | 0.15 | 0.03 |
Mild Steel on Mild Steel | 0.57 | 0.09 |
Chromium on Mild Steel | 0.16 | 0.05 |
Chromium on Cast Iron | 0.15 | 0.03 |
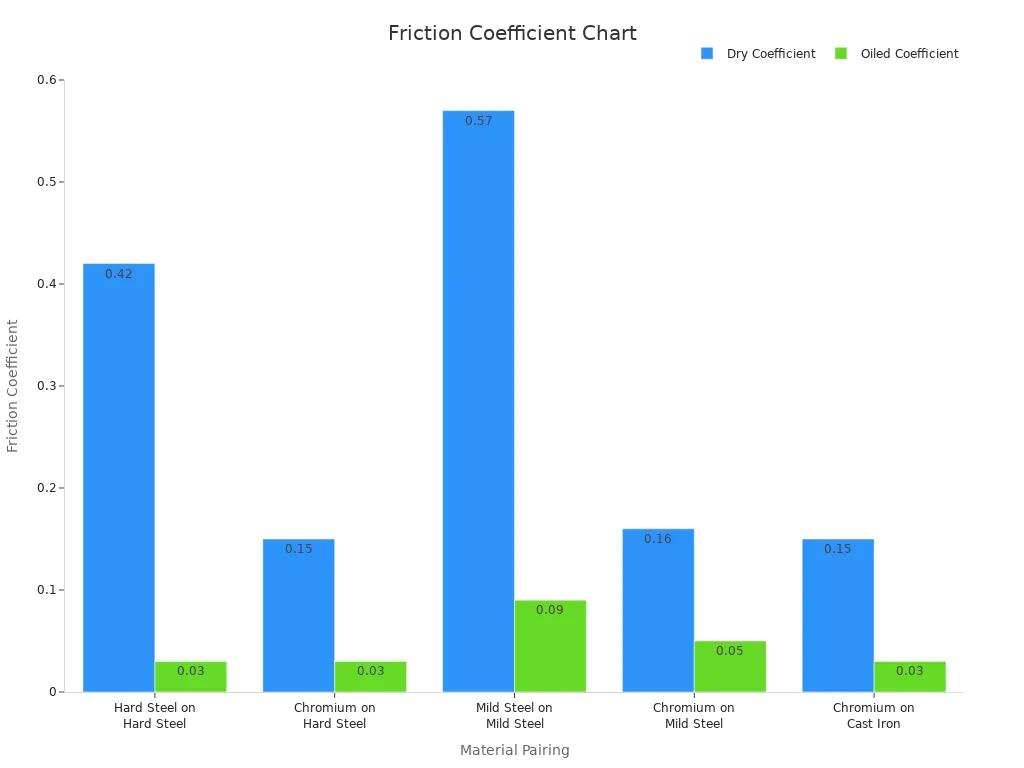
The smooth, uniform surface of hard chrome plated shafts also improves lubricant retention. This feature ensures that moving parts remain well-lubricated, which further reduces friction and supports improved lubrication. Statistical analysis links surface roughness and coating thickness to wear performance, showing that controlling these parameters leads to smoother operation and greater performance and durability.
Hard chrome plating enables equipment to operate reliably in challenging environments. The combination of low coefficient of friction, wear and tear resistance, and corrosion resistance results in extended service intervals and fewer breakdowns. By extending the life of shafts and other components, companies benefit from enhanced durability and consistent operational efficiency.
Cost-Effectiveness Over Time
Companies in industrial sectors often seek solutions that offer both performance and long-term savings. Hard chrome plated shafts deliver significant cost-effectiveness over time, making them a preferred choice for many manufacturers and equipment operators.
- Hard chrome plated shafts last longer than uncoated alternatives. This extended service life means companies replace parts less frequently, which lowers overall replacement costs.
- Maintenance and repair expenses decrease because the shafts resist corrosion and wear. Fewer repairs translate to less money spent on labor and spare parts.
- Downtime drops when equipment runs smoothly. Fewer breakdowns mean production lines stay active, boosting operational productivity.
- Manufacturers can adjust the coating thickness to balance initial investment and expected performance. This flexibility helps companies manage budgets while still achieving high-quality results.
- The shafts maintain their original dimensions, which extends the life of seals and prevents leaks. This feature reduces the risk of costly fluid loss or contamination.
- Salt spray tests show that these shafts can withstand over 500 hours of exposure, proving their durability in harsh environments.
- Improved reliability and a lower risk of sudden failure add further economic value. Companies avoid unexpected shutdowns and the associated costs.
Note: Investing in hard chrome plated shafts may involve higher upfront costs, but the long-term savings from reduced maintenance, fewer replacements, and less downtime often outweigh the initial expense.
The global chrome plating market reflects these economic advantages. In 2023, the market reached a value of USD 17.6 billion. Analysts expect it to grow to USD 24.97 billion by 2032, with a compound annual growth rate of 4.00% from 2024 to 2032. This steady growth comes from rising demand in industries such as oil and gas, automotive, aerospace, and construction. Companies in these sectors recognize that hard chrome plating increases equipment durability and corrosion resistance. These benefits lead to cost savings by extending equipment life and reducing maintenance needs. As a result, organizations see positive returns on their investments in hard chrome plated shafts.
A focus on cost-effectiveness does not mean sacrificing quality. Instead, it highlights the value of choosing components that offer proven performance and long-term savings. Hard chrome plated shafts stand out as a strategic investment for any operation that values reliability, durability, and operational efficiency.
Real-World Industrial Applications of Hard Chrome Plated Shaft
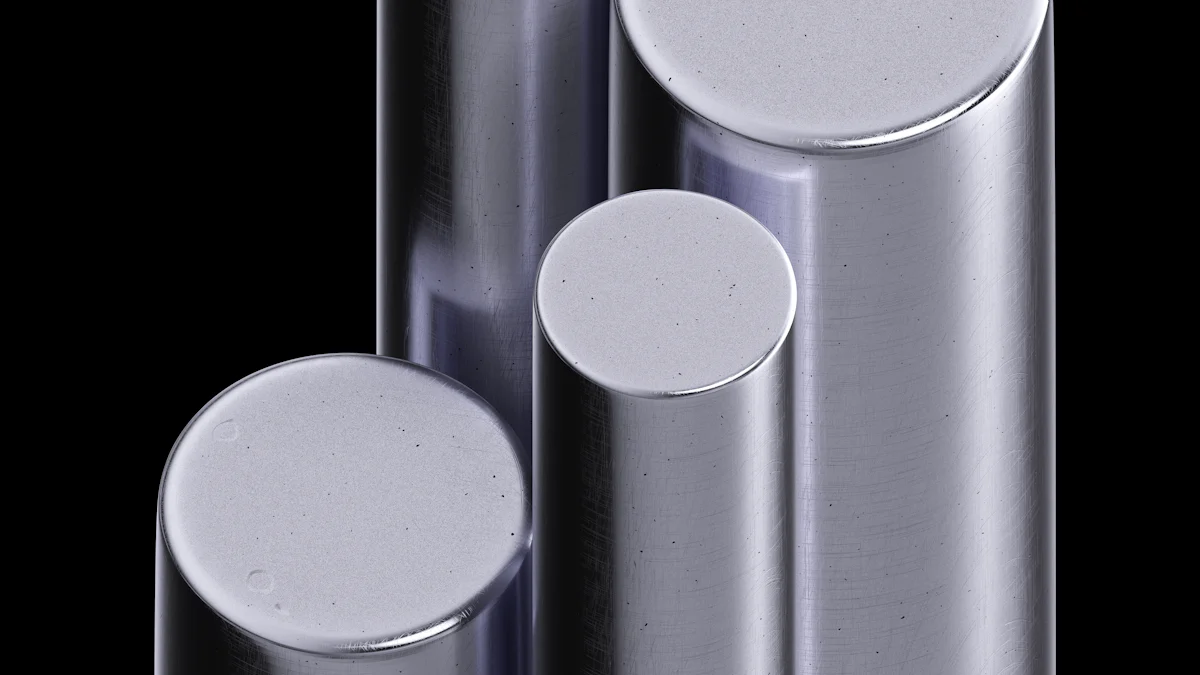
Manufacturing and Automation
Manufacturing and automation rely on hard chrome plated shafts for consistent performance and reliability. Automated production lines use these shafts in shaft press systems, shuttle feed systems, and servo-driven units. Engineers design these systems with safety PLCs, vision systems, and recipe-based controls to ensure precise handling of all parts. The integration of hard chrome plated shafts improves throughput and product consistency. Advanced electroplating techniques, such as pulse plating, create uniform coatings that meet strict industry standards. Quality control methods like X-ray fluorescence and hardness testing verify that each shaft meets the required specifications. These technical controls help manufacturers produce parts with superior wear resistance and dimensional accuracy. As a result, hard chrome plated shafts have become essential in many industrial applications, especially where automation and efficiency are priorities.
Hydraulic and Pneumatic Systems
Hydraulic and pneumatic systems depend on hard chrome plated shafts for their durability and performance. Hydraulic cylinders, rods, and pistons all benefit from the high hardness of the plated surface, which reaches HRC 65-70. This hardness increases wear resistance and extends the life of critical parts. The chrome plating also provides excellent corrosion resistance, protecting hydraulic cylinders from rust and chemical exposure. Microcracks in the plating help retain oil, which reduces friction and energy consumption. Manufacturers can apply the plating in precise thicknesses, ensuring that hydraulic cylinders and other parts maintain dimensional accuracy. The ability to reapply the plating multiple times reduces downtime and maintenance costs. These features make hard chrome plated shafts a preferred choice in industrial applications that use hydraulic cylinders, especially in sectors like automotive, construction, and manufacturing.
Tip: Hard chrome plated shafts in hydraulic cylinders help reduce maintenance frequency and extend equipment service life, leading to lower operational costs.
Heavy Equipment and Construction Machinery
Heavy equipment and construction machinery operate in demanding environments. Hard chrome plated shafts play a vital role in these machines by increasing actuator life expectancy by up to ten times compared to conventional rods. The hard chromium layer provides enhanced wear resistance, allowing hydraulic cylinders and other parts to withstand heavy loads and high pressures. The chromium coating also protects against moisture, chemicals, and harsh conditions. Reduced friction from the polished surface improves hydraulic system efficiency and extends the life of seals. These benefits lead to longer equipment lifespan, fewer repairs, and better reliability in industrial applications. Construction companies and equipment operators trust hard chrome plated shafts to keep their machinery running smoothly, even in the toughest environments.
Automotive and Transportation Industries
Automotive and transportation industries rely on hard chrome plated shafts to improve the durability and reliability of critical parts. These shafts play a vital role in vehicles such as cars, trucks, buses, and trains. Manufacturers use hard chrome plating to protect parts like piston rods, shock absorbers, steering columns, and drive shafts. The chrome layer increases surface hardness, which helps these parts resist wear from constant movement and friction.
Many automotive parts operate under high stress and exposure to harsh conditions. For example, shock absorber rods face repeated impacts and must maintain smooth operation over thousands of miles. Hard chrome plating provides a tough barrier that prevents scratches and dents. This protection extends the service life of parts and reduces the need for frequent replacements.
Transportation equipment, including rail systems and heavy-duty trucks, also benefits from hard chrome plated shafts. These vehicles often encounter moisture, road salts, and chemicals. The chrome layer shields parts from corrosion, ensuring that components like axles and suspension systems remain functional. Salt spray tests show that hard chrome plated parts can withstand over 150 hours of exposure, meeting industry standards for corrosion resistance.
Automotive engineers value the low friction properties of hard chrome plated shafts. Reduced friction means less energy loss and smoother movement of parts. This feature improves fuel efficiency and enhances the driving experience. The uniform surface of the plating also helps retain lubricants, which further protects moving parts.
Note: Hard chrome plated shafts support the safety and performance of vehicles by maintaining the integrity of essential parts in demanding environments.
The use of hard chrome plated shafts in automotive and transportation sectors demonstrates their importance in industrial applications. These shafts help manufacturers deliver vehicles that last longer, require less maintenance, and perform reliably on the road.
Addressing Common Concerns with Chrome Plating
Maintenance and Care Requirements
Proper maintenance ensures that chrome plated shafts deliver reliable performance over time. Operators should regularly inspect shafts for signs of wear, pitting, or surface damage. Cleaning with non-abrasive materials helps preserve the smooth finish and prevents buildup of contaminants. Lubrication remains essential, as it reduces friction and supports the protective properties of the chrome layer. Technicians often use visual checks and surface roughness measurements to monitor shaft condition. When necessary, re-polishing restores the original surface quality. These simple steps help maximize the lifespan of chrome plated components and reduce the risk of unexpected failures.
Expected Lifespan and Performance
Chrome plated shafts offer a significant increase in lifespan compared to uncoated alternatives. Many industrial users report that these shafts last two to ten times longer, depending on the application and operating environment. The high hardness and corrosion resistance of the chrome layer protect the underlying metal from mechanical and chemical damage. Consistent performance results from the uniform coating thickness and strong adhesion. Manufacturers often conduct salt spray and hardness tests to verify durability. By following recommended maintenance practices, companies can ensure that their equipment operates efficiently and reliably for extended periods.
Tip: Regular inspections and timely maintenance help companies achieve the maximum possible lifespan for chrome plated shafts.
Environmental and Safety Considerations
Environmental and safety regulations play a central role in chrome plating operations. Regulatory agencies such as the EPA enforce strict emission limits and monitoring requirements through standards like NESHAP. Facilities must use technologies such as fume suppressants, mesh-pad mist eliminators, and HEPA filtration to control emissions. Scientific studies highlight the importance of managing substances like PFOS, which have been used as mist suppressants and can pose ecological risks if released into wastewater. Advanced treatment methods, including ultrafiltration and reverse osmosis, have proven effective in reducing these risks. Life Cycle Assessments show that alternative wastewater treatments can lower environmental impacts compared to conventional methods. Companies that follow best practices and comply with regulations help protect both workers and the environment while maintaining high-quality production standards.
Max’s Expertise in Hard Chrome Plated Shaft Production
Quality Assurance and Testing Capabilities
Max stands out in the industry by maintaining strict quality assurance protocols throughout the production of hard chrome plated shafts. The company holds ISO 9001-2015 certification, which demonstrates a commitment to recognized quality management systems and consistent process control. Max’s team uses advanced methods to ensure every shaft meets high standards. They monitor temperature, treatment time, and environmental conditions during plating. Surface hardness testing, microstructure analysis, and dimensional verification confirm each shaft’s durability and precision.
Max’s quality control process includes:
- Pre-production inspections to check raw materials and components.
- In-process inspections to monitor production and catch any defects early.
- Final inspections to verify that finished shafts meet all specifications.
- Statistical sampling techniques, such as Acceptable Quality Levels (AQL), to ensure efficient and reliable quality checks.
Operators document every step, from material certifications to inspection results, ensuring full traceability. Regular audits, equipment calibration, and operator training support continuous improvement. These measures guarantee high-quality chrome plating and tight dimensional tolerances, often within ±0.005mm.
Technical Support and Customer Service
Max’s technical support and customer service teams play a vital role in maintaining production excellence. They track key performance indicators (KPIs) to measure and improve support effectiveness. The table below highlights some important KPIs:
KPI Name | Description |
---|---|
First Pass Yield (FPY) | Percentage of shafts produced correctly the first time |
Machine Downtime Rate | Time equipment is unavailable; lower rates show effective support |
Customer Satisfaction | Measures how happy customers are with products and services |
First Contact Resolution | Percentage of customer issues resolved on the first contact |
Cycle Time | Time taken to produce each shaft |
Max’s support team responds quickly to customer needs, provides technical guidance, and helps resolve issues efficiently. Maintenance records and production data help the team minimize downtime and keep equipment running smoothly. By focusing on these KPIs, Max ensures that customers receive reliable products and excellent service every time.
Hard chrome plated shafts deliver proven advantages in industrial settings. They increase longevity by resisting wear and corrosion. Many companies report fewer breakdowns and lower maintenance costs after switching to these shafts. Equipment longevity improves, which means machines run longer and more reliably. Industry professionals value this longevity because it supports consistent performance and operational savings. Choosing hard chrome plated shafts represents a smart investment for anyone seeking durability and reliability.
FAQ
What industries use hard chrome plated shafts most often?
Manufacturing, automotive, construction, and hydraulic equipment industries rely on hard chrome plated shafts. These sectors demand high wear resistance, corrosion protection, and long service life for critical machinery components.
How thick is the typical hard chrome plating on a shaft?
Most hard chrome plated shafts feature a coating thickness between 20 and 100 microns. This range provides optimal wear resistance and corrosion protection while maintaining precise dimensional tolerances.
Can hard chrome plated shafts be repaired or recoated?
Technicians can repair or recoat hard chrome plated shafts. They remove the old layer, restore the surface, and apply new plating. This process extends the shaft’s service life and maintains performance.
How does hard chrome plating affect shaft hardness?
Hard chrome plating increases surface hardness to 68–72 HRC. This high hardness level protects the shaft from abrasion, impact, and deformation during demanding industrial operations.
Are hard chrome plated shafts certified to industry standards?
Manufacturers produce hard chrome plated shafts to meet standards such as ASTM B650, SAE AMS2406, and MIL-C-23422. These certifications ensure consistent quality, durability, and performance in industrial applications.