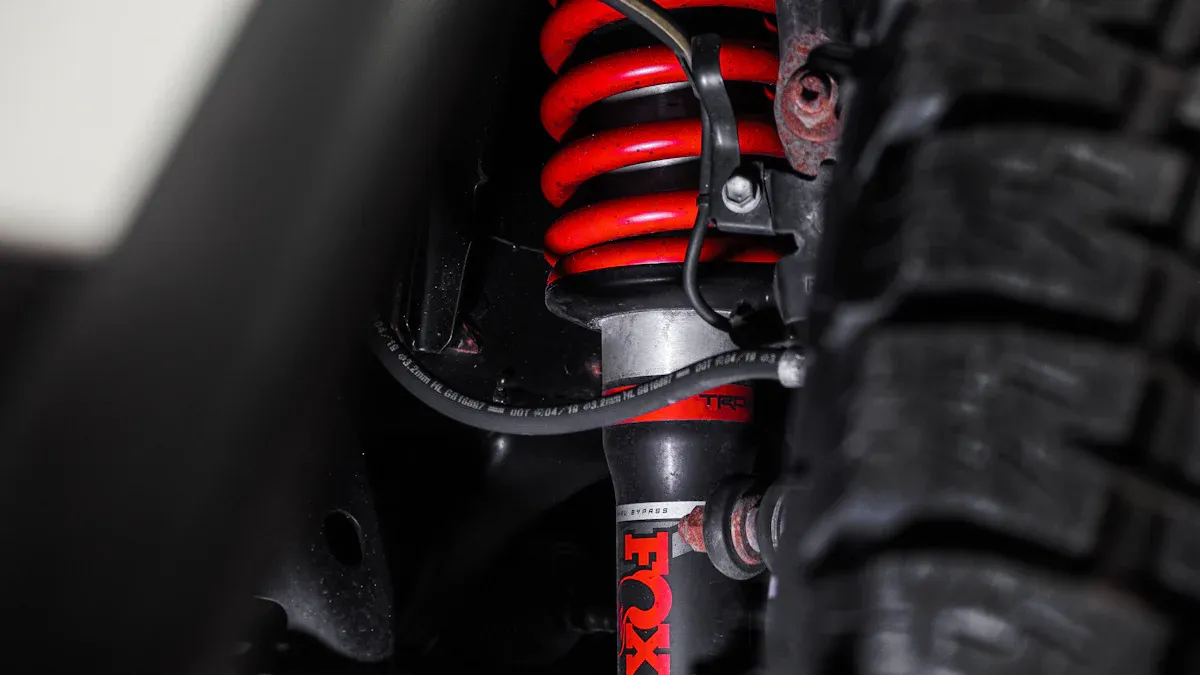
Manufacturers rely on chrome plated steel bar for shock absorbers because it offers outstanding advantages. The chrome plated steel bar provides a protective chrome layer that shields the steel from rust and damage, even in the harshest environments. This material is widely chosen for its exceptional ability to withstand heavy loads and intense pressure. The smooth surface finish of the chrome plated steel bar reduces friction, ensuring longer-lasting parts and improved overall performance. Thanks to these qualities, machines equipped with chrome plated steel bar components operate more efficiently and require fewer replacements over time.
- High strength of chrome plated steel bar supports heavy-duty applications
- Superior corrosion resistance keeps the steel protected
- Smooth chrome plated finish minimizes friction and wear
- Extended lifespan of chrome plated steel bar reduces maintenance needs
Key Benefits of Chrome Plated Steel Bar in Shock Absorbers
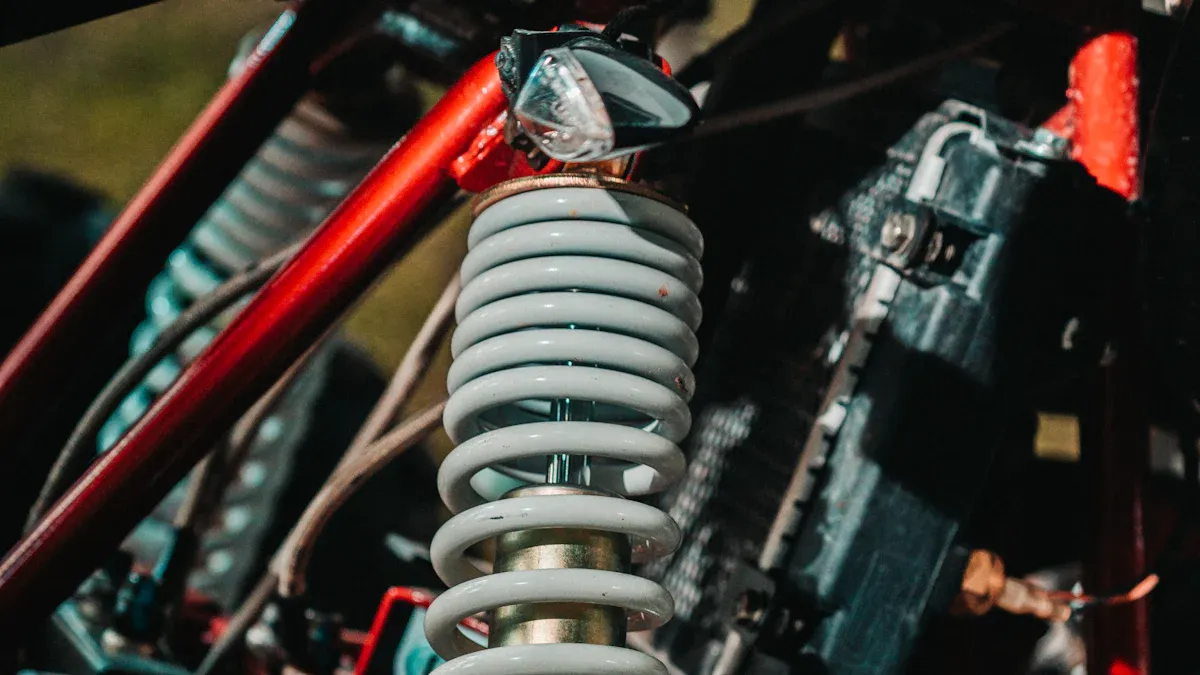
Superior Corrosion Resistance
Chrome plated steel bar offers superior corrosion resistance, making it a reliable choice for shock absorbers in many environments. The chrome layer acts as a protective shield, helping the steel resist moisture, chemicals, and road salts. In laboratory tests, stainless steel bars show lower and more stable corrosion rates than chrome plated steel bars, especially in salt spray and accelerated corrosion tests. Stainless steel contains chromium throughout the alloy, while chrome plated steel relies on a surface coating. Even so, chrome plated steel bar performs well in real-world conditions, especially when enhanced with double or triple chrome layers. These advanced coatings can withstand over 150 hours of salt spray testing, which means the bars can resist rust and maintain their function in harsh climates. This level of corrosion resistance helps shock absorbers last longer and work better, even when exposed to rain, snow, or chemicals.
Tip: Choosing chrome plated steel bar for shock absorbers helps protect against rust and keeps vehicles running smoothly in tough weather.
Outstanding Wear Resistance
Shock absorbers face constant movement and friction. Chrome plated steel bar provides excellent wear resistance, which is vital for these parts. Hard chrome plating creates a tough surface with a hardness of 50–60 HRC, as measured by Rockwell Hardness tests. This hard surface resists scratches and abrasion. In Taber wear tests, hard chrome loses only 2–3 mg per 1000 cycles, showing its ability to withstand repeated contact. The chrome layer also contains microcracks that hold oil, reducing friction and seal wear. This unique structure gives the bar enhanced wear resistance and helps it last longer in use.
Test Type | Result/Observation |
---|---|
Rockwell Hardness Tester | Surface hardness: 50–60 HRC |
Taber Wear Test | Material loss: 2–3 mg per 1000 cycles |
Rotary Wear Tester | Friction coefficient: 0.1–0.2 |
Falex Wear Tester | Durable in lubricated conditions |
Corrosion Resistance | Porosity ≤3 micropores/cm², surpassing AMS 2460 standard |
Dimensional Control | Plating thickness tolerance ±0.005mm |
These results show that chrome plated steel bar stands up to heavy use and keeps shock absorbers working smoothly. The hard chrome surface also helps reduce the need for frequent maintenance.
Enhanced Durability in Demanding Environments
Durability is a key factor for shock absorbers, especially in vehicles and machines that operate in harsh conditions. Chrome plated steel bar delivers high durability by combining corrosion resistance and excellent wear resistance. Triple chrome plating and nickel chrome options can last up to 1500 hours in neutral salt spray tests. Hard chrome plated steel bars used in shock absorbers and hydraulic rods can reach hardness levels of 68–72 HRC. This high hardness, along with strong corrosion resistance, allows these bars to survive repeated impacts, vibrations, and exposure to chemicals.
- Chrome plated steel bar increases the lifespan of shock absorber rods by up to ten times compared to standard rods.
- The hard chrome layer protects against moisture and road salts, keeping the rods strong and functional.
- Reduced friction from the smooth chrome surface helps seals last longer and improves hydraulic efficiency.
- These features lead to an extended service life and lower maintenance costs for vehicles and industrial machines.
Chrome plated steel bar adapts well to different climates and road conditions. Its durability ensures that shock absorbers remain reliable, even after years of use in tough environments.
Precision Chrome-Plated Steel Bars: Essential Properties
High Surface Hardness and Scratch Resistance
Precision chrome-plated steel bars deliver high surface hardness, which is vital for shock absorber performance. The hard chrome layer on these bars reaches values of 69-71 HRC on the Rockwell scale and 900-1100 HV on the Vickers scale. This level of hardness protects the steel from scratches and dents during operation. Precision in the plating process ensures that the bars maintain their resistance to wear, even under heavy loads. The substrate steel usually has a hardness between 32-36 HRC, which supports the chrome layer without causing plating issues. High precision in manufacturing leads to excellent dimensional accuracy, so each bar fits perfectly in its application. This combination of hardness and precision gives shock absorbers a long service life and reliable performance.
Ultra-Smooth Finish for Low Friction
Precision chrome-plated steel bars feature an ultra-smooth finish that supports smooth operation in shock absorbers. The average surface roughness (Ra) achieved on these bars is typically around 0.2 μm, which is ideal for reducing friction. Lower friction means less heat and wear during movement, which helps the shock absorber last longer. The superior surface quality of these bars allows seals to glide easily, preventing leaks and maintaining smooth operation. The final polishing process after plating achieves this high level of smoothness, making the bars suitable for demanding automotive and industrial uses.
Parameter/Process Step | Description/Value |
---|---|
Chrome Layer Thickness | Minimum 20-50 microns (customizable) |
Hardness of Chrome Layer | HV850 minimum |
Surface Roughness (Ra) | Maximum 0.2 μm after final polishing |
External Diameter Accuracy | ISO h7, f7, h8, f8, g6 |
Roundness | Ra ≤ 0.2 μm |
Uniform Plating for Consistent Performance
Precision chrome-plated steel bars rely on a uniform chrome plating layer to ensure consistent performance. The uniformity of the chrome layer prevents weak spots and ensures that resistance to wear and corrosion remains the same along the entire bar. High precision during the plating process results in excellent dimensional accuracy, which is critical for shock absorbers that require tight tolerances. This uniformity supports smooth operation and reduces the risk of failure in demanding environments. Manufacturers trust these bars because they deliver reliable results every time.
Note: Precision chrome-plated steel bars combine high precision, excellent dimensional accuracy, and a uniform chrome plating layer to provide unmatched resistance and smooth operation in shock absorber applications.
Manufacturing Process and Precision in Chrome Plated Steel Bar
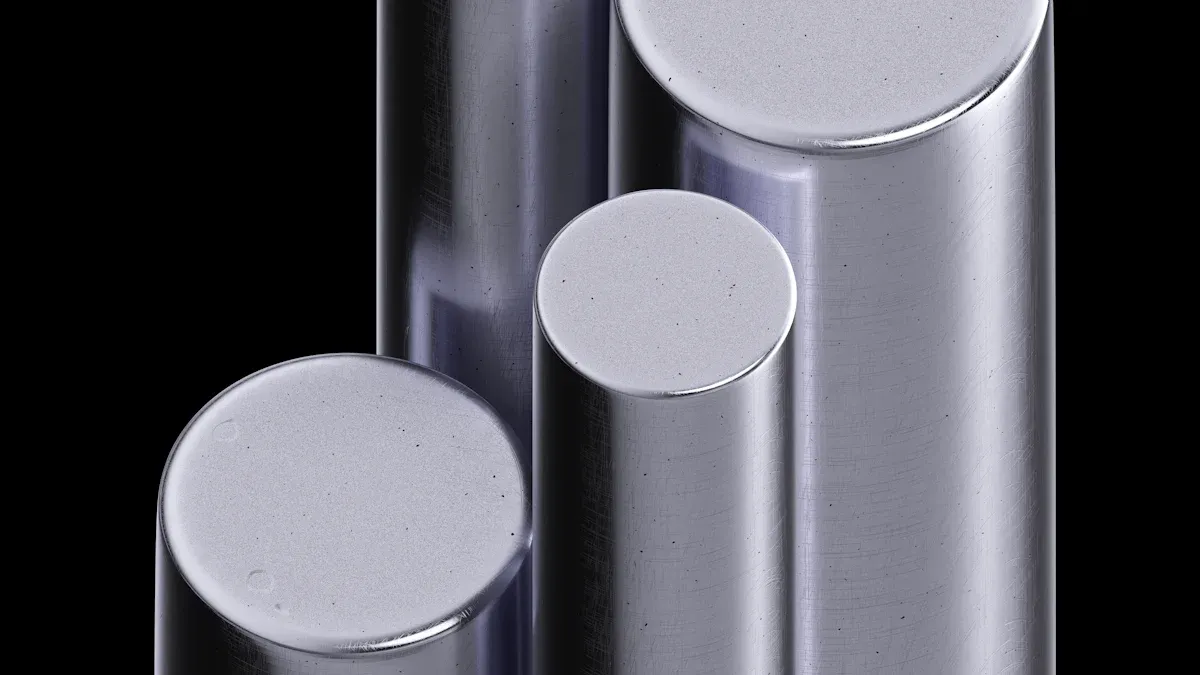
Advanced Chrome Plating Techniques
Manufacturers use advanced chrome plating techniques to create high-quality steel bars for shock absorbers. The process starts with careful surface preparation. Workers clean and polish the steel to remove any dirt or defects. This step ensures a smooth base for the chrome layer. Next, the steel bar enters an electroplating bath. Here, a thin layer of chromium attaches to the surface. This layer improves corrosion resistance, hardness, and surface finish. The chrome plating process requires strict control to achieve the right thickness and uniformity. Precision at every stage helps prevent weak spots and ensures the bar meets industry standards. After plating, the bars go through dehydrogenation and tempering to remove any trapped gases and improve durability.
Quality Control and Testing for Precision
Quality control plays a key role in producing chrome plated steel bars with high precision. Each bar passes through several inspection steps to check for dimensional accuracy and material integrity. Manufacturers use advanced CNC machines and precision inspection devices, such as Mitutoyo micrometers and hardness testers, to measure each bar. The process includes:
- Hydraulic steel raw material cutting
- CNC machining for exact shapes
- Induction hardening for strength
- Chrome plating for surface protection
- Polishing for a smooth finish
- 100% inspection for defects
Certifications like IATF 16949:2016, SGS, and TUV show a commitment to quality. Testing includes thickness, adhesion, and surface finish checks. Performance tests, such as damping force and endurance tests, ensure each bar can handle up to 1,000,000 cycles. Specialized machines, like the Damping Force Tester and corrosion test chambers, help verify that every bar meets strict standards. This focus on precision gives customers confidence in the reliability of each product.
Impact of Heat Treatment and Hardening
Heat treatment and hardening steps greatly affect the mechanical properties of chrome plated steel bars. When heated up to 600°C, the bars keep most of their hardness and do not develop thermal cracks. If the temperature rises above 600°C, cracks can form because the chromium coating and steel expand at different rates. At 800°C and higher, the bars lose much of their hardness, which can lower wear resistance. Forging shapes the metal under high pressure, aligning the grain structure for better toughness and fatigue resistance. Induction hardening increases the bar’s strength, allowing for smaller diameters without losing durability. These steps ensure the steel bars can handle the repeated stress found in shock absorber and hydraulic applications. Precision in heat treatment and hardening leads to longer-lasting, safer products.
Real-World Applications of Chrome Plated Steel Bar in Shock Absorbers
Automotive Shock Absorber Performance
Automotive engineers choose chrome plated steel bars for shock absorber piston rods because these bars improve both ride quality and durability. The 5/8” chrome plated hardened steel shaft resists corrosion and pitting, which helps the shock absorber last longer. Many manufacturers use case-hardened steel with a thick chrome plating layer. This layer is harder than what most competitors offer. A superfinishing process creates a smooth sliding surface. This surface reduces friction and seal wear, which prevents oil leaks and keeps the system reliable. Triple-chrome plated rods add even more strength and corrosion resistance. These features extend the lifespan of suspension components and ensure consistent performance, even in harsh driving conditions.
- Chrome plated bars provide high hardness and wear resistance.
- The smooth finish balances lubrication and friction.
- Enhanced corrosion protection prevents damage from moisture and road salts.
Industry reports show that chrome plated steel bars help maintain smooth operation and reduce maintenance. The plating protects against rust during storage and prevents problems when vehicles sit unused for long periods. This reliability leads to higher customer satisfaction.
Industrial and Heavy Machinery Applications
Chrome plated steel bars play a key role in hydraulic and pneumatic applications for industrial and heavy machinery. These bars are common in hydraulic cylinders and shock absorbers used in mining, agriculture, and marine equipment. The hard chrome plating gives the bars a surface hardness of 68-70 Rockwell C and a low friction coefficient of about 0.15. This combination allows the bars to handle heavy loads and abrasive conditions. The plating also improves load-bearing capacity and precision, which is important for ball joints, bearing surfaces, bushings, and robotic joints.
- Hard chrome plated bars reduce friction and wear in hydraulic and pneumatic systems.
- The bars extend service life and lower maintenance costs.
- Technological advances in plating have made these bars even more durable.
In construction and mining equipment, the chrome plated surface resists high stress and abrasion. The manufacturing process includes rolling, quenching, and tempering, which seal micro-cracks and prevent erosion. These steps help the bars last longer and keep equipment running efficiently.
Reliability in Harsh and Outdoor Conditions
Chrome plated steel bars show excellent reliability in outdoor and marine environments. The chrome plating forms a hard, wear-resistant surface that resists rust and corrosion. Variants like double, triple chrome, and nickel chrome plating offer even greater protection. Nickel chrome plated bars can withstand 1500 hours in neutral salt spray and 500 hours in acetic acid salt spray tests, meeting ISO 9227 NSS and AASS standards.
Type | Material | Hardness (Rockwell) | Manufacturing Process |
---|---|---|---|
Standard Chrome Plated Rods | 1045 steel | RC 15-19 | Chrome Plated Only |
Induction Hardened Chrome Rods | 1045 steel | RC 58-60 | Induction Hardened & Chrome Plated |
Induction hardened chrome plated rods offer superior wear resistance and corrosion protection. These rods are ideal for hydraulic and pneumatic shock absorbers exposed to rain, salt, and extreme temperatures. The use of high-viscosity hydraulic oil and advanced sealing designs helps maintain stable performance in both hot and cold weather. This combination ensures that shock absorbers continue to work well, even in the most demanding conditions.
Advantages of Precision Chrome-Plated Steel Bars Over Other Materials
Comparison with Standard Steel and Stainless Steel
Precision chrome-plated steel bars stand out when compared to standard steel and stainless steel in shock absorber applications. Standard steel offers basic strength but lacks the surface protection needed for long-term use. Stainless steel provides good corrosion resistance because of its chromium, nickel, and molybdenum content. However, precision chrome-plated steel bars deliver a unique combination of high surface hardness, low friction, and excellent wear resistance. The hard chrome layer, with a hardness of 65-69 HRC, creates a smooth, protective barrier. This layer reduces friction and extends the lifespan of shock absorber components. Stainless steel resists corrosion from within, while chrome-plated bars rely on their external coating. Both materials serve well in different environments, but precision chrome-plated steel bars excel in high-cycle, high-stress settings where durability and surface quality matter most.
Cost-Effectiveness and Maintenance Benefits
Precision chrome-plated steel bars offer significant cost savings over time. The hard chrome layer can be reapplied if it wears down, which extends the service life of each component. This feature reduces the need for frequent replacements and lowers maintenance costs. High-quality steel bars with precision chrome plating require less downtime for repairs. Many industries choose these bars because they balance performance and budget. The ability to restore the chrome layer means companies can keep using the same high-strength steel base, saving money and resources.
Tip: Regular inspection and timely reapplication of the chrome layer help maintain peak performance and reduce unexpected failures.
Long-Term Safety and Performance
Precision chrome-plated steel bars provide reliable performance in most automotive and industrial environments. Their strength and wear resistance support long service life. However, extreme cold or highly corrosive conditions can challenge their limits. The following table compares long-term safety and performance among different piston materials:
Performance Aspect | Chrome-Plated Steel Pistons | Titanium Alloy Pistons | Carbon Fiber Reinforced Titanium Composite |
---|---|---|---|
Fatigue Life | ~500,000 cycles | ~1,500,000 cycles | ~2,800,000 cycles |
Crack Growth Rate | 8 μm/1,000 cycles | 3 μm/1,000 cycles | 1.44 μm/1,000 cycles |
Extreme Low Temperature Limit | -35°C | -55°C | -70°C |
Corrosion Resistance | Moderate | Good | Superior |
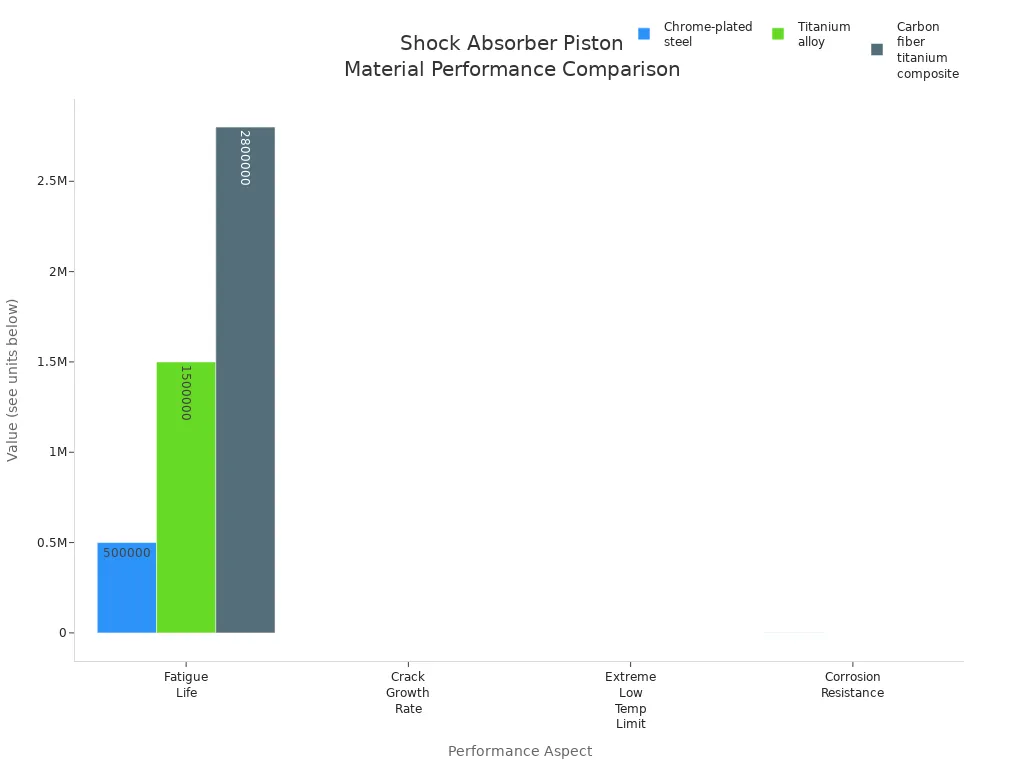
Precision chrome-plated steel bars remain a trusted choice for many shock absorber designs. Their combination of precision, strength, and cost-effectiveness makes them suitable for a wide range of applications.
Chrome plated steel bar stands out as the best choice for shock absorbers. Advanced manufacturing and strict quality control give these bars exceptional durability. Many industries trust them because they last longer and need less maintenance.
- Improved hardness and wear resistance help shock absorbers handle stress and friction.
- Automation and precision coating make each bar more reliable.
- New plating methods support better quality and longer service life.
Choosing chrome plated steel bar ensures durability and top performance in any environment.
FAQ
What makes chrome plated steel bars ideal for shock absorbers?
Chrome plated steel bars offer high surface hardness, excellent corrosion resistance, and a smooth finish. These features help shock absorbers last longer and perform better in tough environments. Engineers choose them for their proven reliability in both automotive and industrial applications.
How does chrome plating improve wear resistance?
The hard chrome layer creates a tough, scratch-resistant surface. This layer reduces friction and prevents damage from repeated movement. In tests, chrome plated bars lose only 2–3 mg per 1,000 cycles, showing strong wear resistance.
Can chrome plated steel bars handle extreme weather?
Yes. Chrome plated steel bars resist rust and corrosion in rain, snow, and salty conditions. Triple chrome and nickel chrome options withstand up to 1,500 hours in salt spray tests. This durability ensures reliable shock absorber performance outdoors.
How do chrome plated steel bars compare to stainless steel?
Feature | Chrome Plated Steel Bar | Stainless Steel |
---|---|---|
Surface Hardness | 65–71 HRC | 20–30 HRC |
Corrosion Resistance | Excellent (with coating) | Very Good |
Wear Resistance | Superior | Good |
Chrome plated steel bars provide higher surface hardness and better wear resistance than stainless steel, making them a top choice for shock absorbers.